
When the Essex MagForceX® Innovation Center set out to develop EnduroTemp® 260+ it was to solve the problem of partial discharge – known as corona – as well as increase the temperature at which a traction motor can operate.
Both were solved, however in doing so, the heat transfer coefficient may also have been improved.
Matt Leach, Head of the MagForceX® Innovation Center, explains that while the heat transfer coefficient improvement may have been an unintended success it brings additional value to the product – but more importantly exponential value to motor designers.
“As you increase the power density or increase the power in that motor, you’re going to have increased heat for the resistance but if you’re able to transfer the heat out faster, it makes the motor more efficient,” he said. “The insulation system will withstand a higher operating temperature, so even while you’re running a little hotter the insulation itself will dissipate heat faster than typical insulations. It will literally allow you to run hotter, longer, with lowered risks of damage to the wire.”
EnduroTemp® 260+ is a product that provides opportunities to designers to maximize power density or apply magnet wires in new high temperature and demanding applications, including variable speed drives.
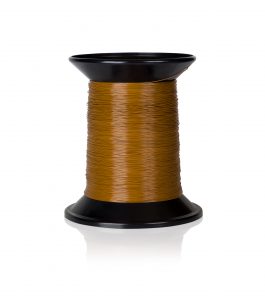
Example of EnduroTemp® 260+
It is an insulation for magnet wire that will extend the life of traction motors in critical transportation applications — that has been specifically designed to withstand higher operating temperatures with an industry best 265℃ thermal endurance. The product will also provide protection to the motor against deterioration created by the modern power electronics controlling the motor. It has an enamel film surface that eliminates ridges present with any tape products because overlaps or gaps are eliminated. The coefficient of friction is also far better versus that on a tape wrapped product, which will allow coils to be manufactured in less time.
EnduroTemp® 260+ is most applicable for use in transportation, but not just traditional vehicles as it can aid greatly in off-road operations, heavy mining equipment, electrified commercial vehicles, and has also proven to be a perfect solution for demanding aerospace applications as well. Other high-temperature windings are going to be subject to a lot of different environments, like eliminating the heat inside of tunnels in European markets or toxic fumes in subterranean workplaces.
“I can see this being used for high heat applications, like motors, alternators, starters that go in any type of high, hot heat climate conditions,” Leach said. “In the past some of those applications have used Polyimide but this is a good, even better, substitute for Polyimide.
“Another key market would be an inverter driven motors, which could be in an industrial motor that’s in a high heat area or it could be in down hole pumps for oil and gas explorations.”
Allan Knerr, an R&D Chemist for Essex Magnet Wire was the principal inventor of the product.
He said that the combination of the three primary benefits working in concert should make for a revolutionary product.
It is one that could change how people think of motor design by allowing them to push what are believed to be the present-day limitations.
“Well obviously the thermal endurance being 265℃ it is one of the highest rated materials, if not the highest rated magnet wire enamel is very exciting. The fact that it survives corona and has such good heat transfer; I am sure the heat transfer coefficient played into the thermal endurance and it should just make life in general better for electrical motor manufactures,” he said. “That just seems like a game winner.”
“You know we are approaching the limits of metal. Copper is good for certain temperature ranges. Aluminum is good for certain temperature ranges and we are closely approaching the use temperature for these materials so I am not sure where it’ll go from here, but each incremental gain we can make will allow us to do more.”
Leach agreed, saying that being able to operate at 265℃, for beyond the testing limits of 20,000 hours will ensure that the products for which EnduroTemp® 260+ is installed, can last beyond the application life requirements.
“It will help make a motor more efficient which will then make the overall vehicle, if it’s going into a car, more efficient. You may get a longer drive time on the same battery or you may be able to have a smaller battery because of the more efficient motor,” he said. “Other parts of the motor would fail first.”
EnduroTemp® 260+ was tested for Dielectric Breakdown Voltage on 12 AWG twisted pairs at an ambient temperature and exceed 11,000 Volts. Its Pulse Endurance test on 12 AWG twisted pairs was stopped after 72hours with no failures as measured per GB/T 21707-2008 test method with 100ns rise time. Its Pulse Endurance test on 18 AWG twisted pairs was stopped after 20hours with no failures as measured per GB/T 21707-2008 test method with 100ns rise time. The Inverter Life test on 18 AWG twisted pairs lasted 294 hours as measured per the Essex MagForceX® Innovation Center UL Certified Wire Test lab. That time frame is three times better than the industry’s nearest competitor.
Chris Richardson, a motor designer and engineer at the MagForceX® Innovation Center said that the numbers that are being produced are simply revolutionary, specifically regarding thermal conductivity.
“We’ve got anecdotal evidence from some our customers saying some of these motors were running 10 to 20 degrees colder,” he said. “For some of these high partial discharge instances, the applications would otherwise need a very thick layer of enamel in order to operate. By making that thermal path more conductive you’re basically getting the heat out more easily with a lot less enamel. This allows the designer to improve the design in several directions including efficiency and power density.
“These major motor manufacturers are going out there for additional thermal conductivity and dielectric training. This is one of those properties that everybody knows they need to get better at and so when you say that there is two to three times the improvement of a standard Polyimide in enamel in terms of thermal conductivity, that means a lot.”
Because EnduroTemp® 260+ is so much better than standard enamels, there could be applications allowing the ability to pack more conductor material in the same space and increase power density. Some applications may exist where a designer may ask for a thinner layer which could produce different results.
Leach said that the list of applications for the product is growing, and that the best way to achieve the desired results is to consult with his team.
“It is hard to do justice to this product in a short conversation, but we have the data to back it all up,” he said. “Someone with a background in electrical engineering or motor design will want to see what was done and what can be done, and we welcome those discussions.”
“Our market experts are bringing up ideas for new applications on what seems like a daily basis and that is exciting. We know the technical side, but I believe we are just scratching the surface on ways that EnduroTemp® 260+ can be used.”
View more solutions for EVs, Hybrids, and other electrified commercial vehicles.